Timber-frame construction is fast becoming the most popular option for self builders, but there are still a lot of myths surrounding it, and these can lead to concerns about the pros and cons of timber-frame homes. In fact, the advantages of timber-frame construction vastly outstrip the disadvantages, and many things including the speed of build, sustainability, energy efficiency, and more all contribute to how good timber-frame construction really is.
1. Fast Build Time
Closed-panel timber-frame construction is an offsite method of construction, which means the panels are prefabricated in our factory before being assembled onsite. This gives rise to an extremely rapid construction time; the whole superstructure can be up in as little as two to three weeks.
2. Reduced onsite labour - Less for you too manage
Sustainably managing resources like food, minerals, energy, and services, such as biodiversity, tourism and culture is linked to our ability to assess and predict the impacts of human activities on marine ecosystems. Getting this right under current and future climate change is key. It is also challenging as impacts on marine ecosystems are extremely variable and subject to large uncertainties.
In addressing these challenges, MISSION ATLANTIC will reduce such uncertainties and aim to inform decision makers about the likely consequences of different management measures and strategies, with clear mandate from end-users.
3. Low waste volume - Reduce Environmental Impact
Reduced time onsite not only reduces site labour, it also lowers the environmental impact and disruption to local residents that a building site might incur. There is significantly less waste at a timber-frame construction site than at a masonry one, because the bulk of the manufacturing does not take place in situ, but in the factory. This means there is a low volume of waste onsite requiring removal, which is not only better for the environment, but also saves you money on hiring multiple skips for waste removal.
4. Weathertight – Start Internal Work Sooner
Within our timber-frame kit we offer an optional Weathertight Package to make the self-build process even easier. This will deliver the superstructure to a secure, weathertight stage, allowing internal works to begin sooner and ensuring a single point of responsibility for the entire build up to this stage.
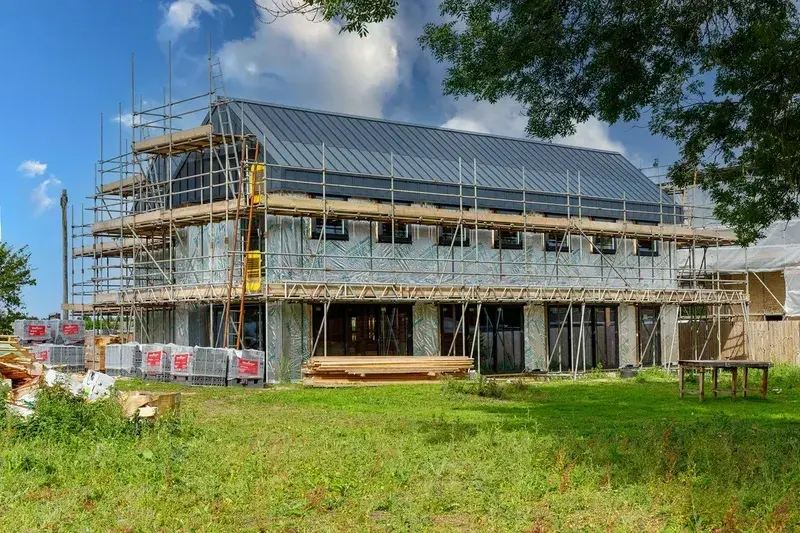
5. Reduced Thermal Bridging
Thermal bridging, also known as cold bridging, is the name given to points of heat loss in a building envelope, usually focused on junctions where two components are joined together. Thermal bridges within a building affect its thermal efficiency, and a poorly insulated structure will mean higher energy bills and a lower overall thermal efficiency.
With masonry construction, there are joins between every single block, offering innumerable opportunities for heat to escape. Conversely, a timber-frame panel is a much larger surface area with far fewer junctions, and we use a continuous insulative lining to reduce instances of thermal bridging.
Kingspan ULTIMA® demonstrates a level of performance that far exceeds SAP guidelines, achieving thermal bridging values of 0.03-0.04. SAP calculations help to define the Energy Performance Certificate (EPC) of your home, which in turn is used to help determine the value of a home, so achieving such excellent thermal values is hugely beneficial. With Kingspan ULTIMA®, your EPC will measure on the high end of the scale, adding value to your property should you desire to sell it in the future.
6. Excellent Thermal Performance - Save Energy And Reduce Your Bills
The excellent energy performance of timber-frame construction is not limited only to thermal bridging, either. Timber frame has a lower embodied energy than other mainstream construction methods like masonry or steel. This means that far less energy is required for its cultivation, extraction, and processing into a building material.
Houses built with timber frame achieve lower U-values compared to brick builds of an equivalent wall thickness, significantly lowering heating costs and the home’s carbon footprint.
Closed-panel timber frames are inbuilt with insulation, and this consideration of thermal performance at the minutest of levels is known as a fabric-first approach, offering lower rates of thermal bridging and achieving excellent airtightness levels. Not only will these lower your fuel costs and help achieve a comfortable internal environment, it will also contribute to your home’s overall energy efficiency.
7. Closed Panel Timber Frames are Load Bearing – Greater Design Flexibility
Closed-panel timber frames are lightweight, composite panels, allowing for taller ceilings and larger spans. This will give you greater flexibility, particularly regarding open-plan areas, allowing for more freedom when designing. As the frames are designed and manufactured to fit the specified dimensions of the design, architectural drawings can be precise, making your dream home a reality.
8. Closed Panel Timber Frame is Slim – Increased Floor Space
Another key advantage of timber-frame construction is its slim wall build up. Closed-panel timber frames have insulation built into the panel itself, whereas a material like brick and block requires many more layers of insulation to surround it. The result is a timber-frame wall that is thermally efficient and slim; to reach the equivalent level of thermal performance, a masonry wall would have to be significantly thicker.
Using timber frame will free up much more internal room for you to enjoy. Shaving off inches from every wall may not seem significant, but can add up to an overall space saving of metres. One of the key methods in property valuation is assessing the amount of internal floor area; more space means the home is worth more.
With fully outdoor construction methods like masonry, the bulk of the work has to occur onsite, which can lead to problems with stopping for wet weather or relying on multiple deliveries of different components. These delays will have a knock-on effect, not only on your build schedule, but on your budget, and can lead to a lot of stress.
As timber frames are part manufactured offsite, this provides you with greater cost certainty because there are far fewer variables to contend with. This will allow you to set out an accurate build schedule from which it’s highly unlikely your project will deviate.
Even if there is wet weather onsite, timber-frame construction is a ‘dry’ form of construction, meaning work can continue regardless. As a customer, your economic risk factor when you opt for timber frame is far lower than other build methods.
9. Sustainability - Reduce The Carbon Footprint Of Your Build
All of the timber we use at KTS, from the wood we use in our timber frames to the chippings that make up our OSB, is sourced from sustainable forests. These offset tree loss by planting many more trees than are cut down, and are certified by an independent chain of custody, which checks them on a yearly basis to ensure the tenets of sustainability are being upheld.
Timber is also one of the few sustainable resources used in mainstream construction – the manufacture of bricks and concrete rely upon raw, finite materials. Timber has a significantly lower carbon footprint than, for example, steel, because it requires far less energy for cultivation, extraction, and manufacture. In fact, the sustainable forests act as carbon stores and create valuable ecosystems for local flora and fauna.
10. Factory Quality - Controlled Conditions For The Best Finish
Compared to a fully onsite fabrication, with timber-frame construction the quality is much higher. Each frame is designed exactly to fit the specific house design, which is computer controlled, and then the frame itself is manufactured in our factory according to these dimensions. This means that dimensional accuracy and high quality are standard for timber-frame construction. Efficient, controlled manufacturing also results in less site waste and a more efficient use of material.
Summary
Is Timber Frame Good for a Self Build House?
Timber-frame construction is standard practice in many countries worldwide, and its obvious benefits are becoming more well known in the UK. As we look to materials that are sustainable and energy efficient, timber frame will only increase in popularity. Timber-frame construction benefits everyone at every stage of the construction process: architects have more design flexibility, tradespeople can begin sooner, and you will have a home that’s energy efficient, fast to build, and has a low carbon footprint.