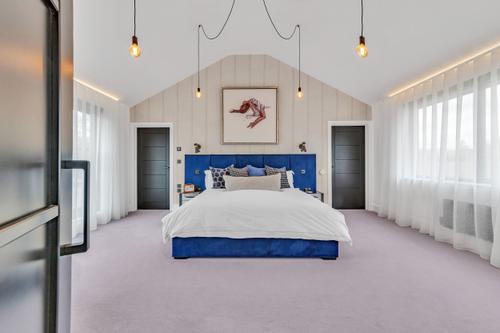
The project
Peter and Sophie Hill’s first foray into self-building came about as rather a happy accident when they realised it would be better to demolish the existing bungalow on their plot and start again.
“We didn’t originally plan to self-build. We bought the bungalow because we liked the plot and we were going to convert it, put a timber-frame first storey on it and extend it” explains Peter. “I finally got the quote in and talked it through with the architects and we decided it would make more sense financially to knock it down.”
The couple had been searching for a renovation project for a while. They were looking to downsize as a step towards retirement and were renting a friend’s flat, having sold their house in Esher. “We were looking for months. It felt like forever,” laughs Peter.
They even considered a new build, but the spec was never quite right. Finally, they found what they were looking for. “It’s a big plot, almost a quarter of an acre, and just had a two-bedroom bungalow on it, which kind of didn’t make sense,” he says.

The evolution of their self build
The Hills engaged an architect to draw up plans for the renovation and extension that incorporated the features they wanted in their home – lots of glass, bifold doors opening to the patio and garden, and a huge master suite with large bedroom, walk-in wardrobe and shower. “He designed something that gave us what we wanted based on the footprint that we already had, and we got that through planning,” explains Peter.
When they realised it was going to be more cost effective and efficient to knock down the existing property and build from scratch, they made minor alterations to the plans already approved – adding in a double-height entrance hall and galleried landing – then resubmitted them.
“We knew from neighbours who'd gone through planning themselves that they wanted the design of anything new to reflect what was already on the close,” says Peter. “Ironically, of course, the house looks nothing like any of the other houses on the close, although it was based on the original. The planning officer came around and said she liked the design, and they were happy with the materials.”
The result is a contemporary style with white render, cedar cladding, and a black slate roof. It occupies the same footprint as the original property, but with advances in building techniques, is better insulated and more energy efficient – and is worth more.
The relationship with KTS
Peter and Sophie decided to partner with KTS after seeing the company at a self-build show. They did consider other companies but Kingspan’s size appealed to the couple. “We liked the professionalism, the fact that they were big so had financial backing,” explains Peter.
Despite a few delays, the build progressed smoothly. Kingspan provided the frame, unfinished roof, insulation and soundproofing, Peter and Sophie then hired subcontractors for the windows, roof tiles, and floors, as well as for the internal and external cladding.
Their project manager sourced trades for plumbing, electrics, and decorating. He was on site a couple of days a week and had access to a wide range of contractors. At the same time, they were in continuous contact with their KTS contracts manager and a couple of his colleagues. “We were able to talk about anything around engineering that might have been an issue, or confirming details like window openings, so that we could get the correct specifications to our window contractor,” says Peter.

Looking back and looking forwards
Overall, the self-build process went smoothly, taking around four weeks longer than originally planned, “which is, in the greater scheme of things, not really a major issue,” says Peter.
The experience has taught him that, were he to self-build again, he would use a prime contractor rather than an independent project manager. He says: “I ended up managing too many things, I think.
“A prime contractor has to deliver to the design schedule and spec, notwithstanding any issues that might crop up, and it would probably cost a bit more but I think it's a better approach, at least for us, from a risk management point of view.”
The couple found there were a lot more decisions to be made than they’d envisaged, with decision-making on an almost daily basis, which could be exhausting – but which was also the best part, says Sophie. “The best bit is it’s all your own decisions. You’re not listening to, or working from somebody else’s ideas.”
Their new home is valued at 30% more than they spent on it, he says. “We were happy with that.”
So is another self-build on the cards? “We’ve been toying with the idea,” admits Peter. And the best bit about self-building? “Moving in, when it’s all over,” he laughs.
The new house
Demolition began in October 2020 and the Hills moved into their new home in June 2021. It has everything they envisaged: a substantial master suite upstairs with a very large bedroom, dressing room and en suite shower room, and a further two bedrooms and family bathroom.
Downstairs, on one side of the house there’s an open plan kitchen, dining and living area, and a boot room; on the other side there’s a large room currently used as a gym and cinema room, a guest suite with bedroom, dressing room and en suite shower, a cloakroom and a utility room.
“It’s fantastic, very easy to look after, airy and really big,” says Sophie.
Bifold doors in the kitchen open to the patio and garden, which was landscaped when the building work had finished. The couple decided against a garage, but the driveway is large enough to accommodate six or so cars.
The expansive use of glass gives the house a spacious, light-filled feel, which is only enhanced by the entrance hall that stretches the entire width of the house, to the garden.
“I love the hallway and the double height, you walk in and you can see right through to the garden,” enthuses Peter. “So right in front of you at the end of the wide hallway is all glass, just as you walk in it’s full of light. The landing has the same size window from the back, it all just feels very grand.”
Their new home helps with energy efficiency and has a very high SAP rating. An air source heat pump supplies underfloor heating downstairs and radiators upstairs, there’s no gas to the property, partly for energy efficiency and partly because of Government plans to phase out gas boilers. However, the couple didn’t install solar panels. “We decided not to on the grounds that we wouldn’t be here long enough to see a return,” says Peter. “We are going to downsize – our retirement plan – eventually.”
For Sophie, shopping for everything – windows, kitchen, bathrooms and décor – was a big highlight, while for Peter, the process of deciding where everything was going to go, was a big part of the experience. For both of them though, seeing the frame going up had the greatest impact. “That was impressive, says Peter. You go from a concrete slab to an almost fully formed building in about five weeks.
“You don’t get that from a brick build.”
Published June 2024